Roof flashing technique is used to prevent water leakage from the roof. It is a sheet made of metal and which requires installation at roof valleys/ gutter, chimneys, skylights, ridges, roof-wall intersections of the roof. The roof flashing is usually made from rust resistant metals like galvanized steel, aluminum or copper. It may be fabricated from plastics, roofing felts, or rubber etc.
Galvanized sheet metal roof flashing is widely used roof flashing whereas Aluminium and Copper roof flashings are used where cost of maintenance matters. Copper is the most durable but it is costly and has advantages over the other metals as the corners of copper can be soldered to make the joints water tight. This article tells you about roof flashing locations, roof leaks testing, roof flashing materials, and types of roof flashing.
How to test roof leakage for roof flashing?
Roof leakage testing is a way to find the place and cause of leak in the roof of your house. Wait for dry weather and ask one person to go onto the roof with a garden hose while the other person to go inside the attic with a bucket and strong light. The person on roof floods the roof with water while the other person watches carefully until the leak appears into the roof. Once the leak is found, drive a nail into the hole to mark the location of leak.
Where to apply roof flashing on roof?
Roof flashing is fixed at roof top edge, pipes, chimney, and edges resting on the wall, skylights, and valleys / gutter and at the joints of top roofing sheets/slates to fasten them against water penetration or leakage. The roof flashing protects building from water leakage and dampness and ensures the safety of materials and contents of the building against water leaks.
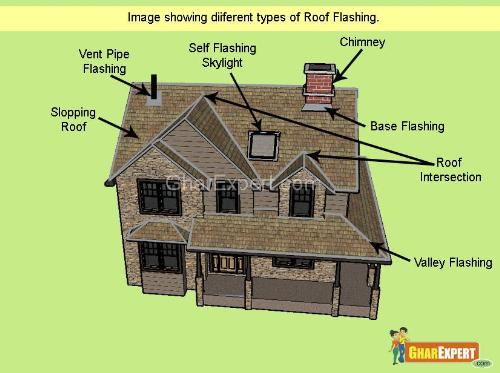
Roof Flashing Types
Chimney Flashing
Chimney flashing is installed around the base of chimney to protect house from leakage. This flashing is fixed where walls of chimney rest on roof shingles. It has been categorized in two parts i.e. Cap flashing and Base flashing.
Cap flashing is provided at projection or with walls at the point of intersection of walls and roof shingles. To avoid leakage of water, 15 cm to 20 cm cap flashing is overlapped on Base flashing. A groove is provided in wall or parapet to fix Cap flashing. To avoid wind pressure and strengthen the edge of flashing, the edge of Cap flashing metal sheet is bent from 12 mm to 25 mm.
Cap flashing is installed on the slope of the roof. Along the slope of roof Cap flashings are arranged in steps where upper steps overlap the lower steps at least by 15 cm to avoid any leakage. Base flashing should be inserted in such a way on the roof consisting of slate, tiles or asphalt shingles as the joints are water tight living no possibility of leakage.
To avoid differential movements caused by change in weather, fix Cap flashing and Base flashing independently. If the flashings are improperly fixed or installed carelessly, they may be damaged by ice or storm. If both flashing are bent up to each other at the joint, they will not move properly according to weather changes. To avoid leakage the joints should move freely but care should be taken that these joints are tight.

Continuous Flashing
This flashing is applied to protect the joints of
vertical wall and sloped roof. The rain water from the slope of the roof drains out from the building but some quantity of water leaks through the joints of roof and wall creating leakage.
To avoid the leakage at the edge of vertical wall and roof, continuous flashing is used.
Drip Edges Flashing
This flashing prevents water seepage along the edges of rakes and eaves. Drip edge flashing is used under roofing felt adjacent to eaves and over roofing felt adjacent to rakes.
Skylight Flashing
The joints around skylights are covered with skylight flashing at the base and step flashing on the sides to avoid leakage.
Step Flashing
Stepped flashing is used where a sloped roof meets a masonry wall.
To prevent leakage from the sides of walls, skylights, chimney, step flashing is used. These flashings are installed at right angle, connected the roof tops and walls of the structure. The vertical edge of flashings is usually embedded into the wall so that the water can’t leak behind it.
Valley Flashing
Valley flashing is provided at the joints where the two roofs meet to protect roof from leakage. The channel/gutter is provided on the supports to drain out rain water from the roof.
Vent Pipe Flashing
Vent pipe flashing is fixed over chimneys and pipes. It comes in the
shape of cone with a flange at the base and works into the shingles when the roofing is applied.
Roof Flashing Materials
Roof flashing should be tough, rust-proof, weather proof, low in maintenance and accommodate weather changes.
Roof flashings are fabricated from metals like
Aluminum, Copper, Galvanized Steel, Lead coated Copper, Stainless Steel, and Zinc which are rust proof, tough. The flashing is also available in plastic, rubber, roofing felt etc. The following are some roof flashing materials.
1. Galvanized Steel Roof Flashing
You can make this
roof flashing by coating steel sheet with a layer of zinc alloys. Use galvanized nails while fixing galvanized steel flashing as fasteners of different metal will corrode soon. The flashing should be bent mechanically for good results.
Advantages of Galvanized steel roof flashing
- Economical material
- Gives a better look
- Less fabrication and installation cost
- Available in long pieces that can be fixed quickly
Disadvantages of Galvanized steel roof flashing
- Rust and decay in short time if used without paint
- Bad effect in polluted and acidic environment
- Not molded into any shape easily
- Needs heating for molding to the required shape which spoils galvanizing
2. Stainless Steel Roof Flashing
Stainless steel is durable flashing material specially suited for tough and corrosive environments. It is good to fix on valleys and counters. It is formed as per site requirement as it is not available in preformed shape. Stainless steel nails should be used while fixing these flashings.
Advantages of stainless Steel roof flashing
- Most durable
- Can be turned into any shape
- Not affected by ecological corrosion like acid rain or salt spray
- Not spoiled if fixed in direct contact with masonry or concrete surface.
Disadvantages of stainless Steel roof flashing
- Costly
- High labor for fabrication and installation
- Difficult to shape in the field being stiff and rigid material
3. Copper OR Lead Coated Copper Roof Flashing
Copper is one of most durable and rust proof material. It requires technique to cut, design, fabricate and install. This flashing also needs skilled and experienced craftsman for proper installation.
Advantages of Lead coated Copper roof flashing
- Long life
- Weather proof
- Low maintenance cost
Disadvantages of Lead coated Copper roof flashing
- Costly material
- Expensive fabrication and installation
4. Aluminum Roof Flashing
This
roof flashing is
durable and versatile and can be fixed around chimney, vent etc. It is available in various thicknesses. You can increase the life of this
roof flashing by painting or anodizing. Aluminum can be turned into any shape easily according to requirement. Thick aluminum flashing has no reaction in salty and corrosive environment. The fastener of any other material may be harmful to
aluminum roof flashing which is easy to install.
Advantages of Aluminum roof flashing
- Economical in comparison to copper
- Inexpensive fabrication and installation
- Soft in nature and can easily be molded in any required shape.
Disadvantages of Aluminum roof flashing
- Spoiled in short time if it is used without painting or anodizing
- Handled carefully being soft in nature otherwise leakage may start
5. Rheinzink Roof Flashing
Rheinzink flashing consists of 98% high grade zinc and 1 % copper and 1% titanium alloys. It is available in sheets and has natural blue grey or grey green color. It can be painted.
Advantages of Rheinzink roof flashing
- Works easily into complex shapes
- Less expensive than lead-coated copper
Disadvantages of of Rheinzink roof flashing
- Requires ventilation to protect the underside of material from white rust and corrosion which reduce its life
- Needs bituminous material to reduce the influence of alkali, acid etc.
;